Building a Porch Part 2 | MAD County Standard | Part 12
- MR Post Frame
- Dec 27, 2023
- 3 min read

Hey there! Welcome back to Mr. Post Frame. We are back here at the MAD County Standard build and we're about to dive into the second part of our porch framing project. The MAD County Standard is a smaller version of our very own home. It is a 3 bedroom, 3 ½ bathroom, 2,300 square foot barndominium. But before we get into the nitty-gritty of that, I've got some exciting news for all you self-building enthusiasts out there. If you're passionate about self-building, make sure to check out our Patreon community. It's a fantastic space where we delve into various self-building topics each month, host live sessions, and connect with like-minded self-builders. And hey, if you're looking for some expert assistance in designing your post-frame home, shop, or garage, just shoot us an email at design@mrpostframe.com. Now, let's roll up our sleeves and get back to the porch.
As of now, we're still hard at work on the front side, meticulously cutting the pieces to bring our porch vision to life. The star of the show? An eight-foot-wide A-frame structure that's going to add both functionality and aesthetic appeal to the space. Allow me to guide you through the detailed process.

For this A-frame, I'm strategically centering it over two posts, precisely 96.5 inches apart, making each side a neat 48.25 inches. The magic number here is 45 degrees—every cut, every angle, follows the calculations of the Pythagorean theorem. It's all about precision to ensure a perfect fit and a robust structure. Now, once we've got the A-frame pieces cut and ready to roll, our attention shifts to the sub-rafters. Picture this: we're using 2x6s, hanging them securely to the wall, ensuring nothing short of a rock-solid structure. The overhang calculation involves adding 10.5 inches to an already solid 8-foot length. Now, here's the twist—we're experimenting with 2x12s for sub-rafters and dropped purlins, breaking away from the traditional method of placing purlins on top.
The 2x12 rafters nicely tie into the house structure, and we're adding extra support with well-placed blocks and metal brackets, gearing up for any potential uplift resistance. As we progress, the strategic placement of plywood becomes pivotal, setting the stage for future spray foam insulation.
Let's switch gears and talk about the porch roof. We're embracing an overhang bracket system for dropped purlins. This method gives us the flexibility to achieve that perfect overhang without compromising any of the structural integrity.

Now, when it comes to sheathing, we're prioritizing the rough exterior, crafting a shield against the elements, particularly snow. It's a strategic move to ensure the longevity and durability of the structure, not to mention making the installation process smoother.
Now, let's talk about the full cost breakdown of this porch. We're estimating the overall cost to be around thirteen thousand dollars, encompassing framing, metal, and a four-inch slab. However, it's crucial to note that labor costs can be a bit of a chameleon, varying based on your location and the specifics of the project. As a rule of thumb, you can generally anticipate labor costs to hover around double the material expenses.

In essence, what we're crafting here is a porch that seamlessly fuses traditional craftsmanship with innovative techniques. Stability and efficiency are our guiding principles, ensuring that this porch not only stands the test of time but also elevates the overall aesthetic of the space. If you've got burning questions or simply want to share your thoughts on this porch framing journey, feel free to drop them in the comments below. Thanks for tuning in, and we'll catch you in the next post.
Thank you,
MR Post Frame
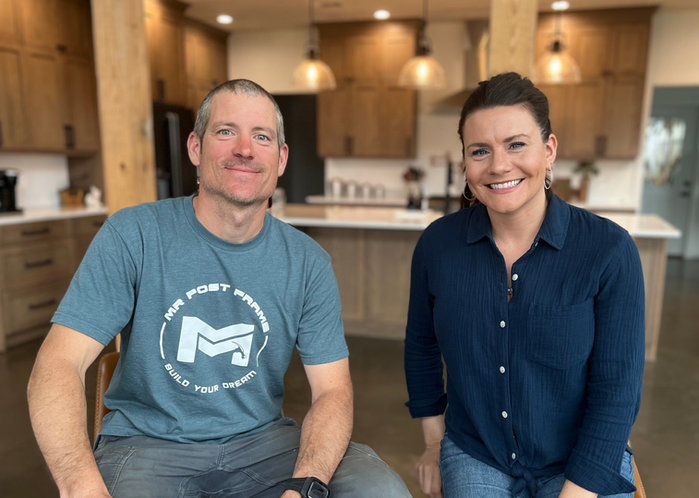
Patreon Group:
Interested in tackling your build on your own? If you want to explore the possibility of being your GC or self-building, our Patreon membership is for you! It's a community of like-minded people offering support, discounts, Q/A, and more.