Barndominium Underground Plumbing | MAD County Standard | Part 7
- MR Post Frame
- Dec 18, 2023
- 3 min read
Updated: Dec 19, 2023
Guys, welcome back to the show! Let's dive into the current state of our barndominium project. Our structure is solid, with plywood sheathing on the roofs. The only problem – they're currently blanketed in a layer of snow, halting our progress in putting the metal sheets on. Despite this setback, our determination is unwavering. The primary goal is to pour the concrete, and to get there, we're diving into the realm of underground plumbing, rough-in electric conduit, and water line installations.

Picture this: the structure is set, the gravel is in place, and we're about to lay out meticulous string lines. These lines are our guides for precisely placing finished walls. Tomorrow, the trenches will be dug, and the pipes will start weaving their way through the ground. The groundwork for this – an entire day spent scouring various stores to procure all the necessary plumbing materials.

Let's delve a bit into the technicalities of these string lines. Measurements are crucial; for instance, the toilet on the inside wall is meticulously calculated to be seven feet three inches from the designated string line. Likewise, the toilet on the outer wall is slated for a position at nine feet ten inches. These intricacies are not just numbers; they are the key to a flawless plumbing setup.
Moving forward, our string lines serve an important purpose. They guide us in marking where plumbing will emerge, acting as beacons for the finished side of the walls. This precision is indispensable when determining the exact spots for drains and vents. Each fixture, be it a toilet, sink, or shower, is strategically placed based on these carefully drawn string lines.

Now, let's embark on a more detailed plumbing walk-through. The main drain and waste pipe take center stage, running perpendicular to the walls. This deliberate placement allows for seamless branching for various fixtures like toilets and sinks. A strategically placed cleanout ensures easy access, and the main line gracefully branches into smaller lines catering to different sections of the house – typically using a four-inch schedule 40 main line.
String lines remain our guide, helping mark where finished walls will stand and aiding in the precise placement of vents and drains. For specific fixtures like toilets, sinks, and showers, we break off accordingly. Vents are positioned meticulously to guarantee optimal drainage and ventilation.
Transitioning to water distribution, we've opted for a home run system featuring a manifold tucked neatly under the floor. This ensures that each faucet boasts dedicated hot and cold lines. PEX tubes snake their way beneath the floor to deliver water precisely where needed. Of course, insulation is a non-negotiable, and measures are taken to shield these vital lines during the concrete pouring phase.

Electricity, too, has its role in this process. Conduits, using schedule 80, work their way outside the structure, providing a streamlined path for the electrician to pull the necessary lines. Even the garage doesn't escape our attention, with drains carefully installed, daylighted if local regulations permit.
While it's crucial to mention that I'm not a certified plumber, my experience in extensive plumbing work on personal projects adds a layer of practical insight. It's worth noting that the labor cost for this plumbing work is likely lower than hiring a professional plumber, but seeking professional advice is always a good choice.
Thank you for joining us on this detailed journey into our project. In our next part, we'll explore the fascinating realm of in-floor heating, covering vapor barriers, insulation, tubing, and much more.
Thank you,
MR Post Frame
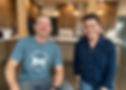
Patreon Group:
Interested in tackling your build on your own? If you want to explore the possibility of being your GC or self-building, our Patreon membership is for you! It's a community of like-minded people offering support, discounts, Q/A, and more.